Library of interesting images and discussion related to pump and irrigation problems,
amateur installations, and general poor practices to be avoided
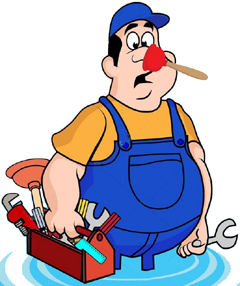
"Pinocchio Brandy"
One of our competitors websites claims the founder is a plumber ? If so, the information we received indicates he no longer shows up on any jobsite, and he never scuba dived any pump install.
This company and in fact ALL of our competitors openly admit they install brands of pumps using Chinese motors. Some try to hide it, but if you insist to inspect the body of the submersible pump motor they plan to install you will see "Made in China"
Lake Travis Lake Pumps has sufficient inventory of American made Franklin and Grundfos pumps - - the best in the business.
Some background: the Xylem/Centripro/Gould's/ITT/Red Jacket, Sta-Rite, and others were exclusively using Franklin motors for decades before they all mistakenly converted to obtaining their 4" motors from a Chinese motor factory known as “Faradyne”.
c
c
Below shows all it takes to cause a submersible lake pump to fail.
Our trade secret, proprietary new screening method on our custom pump shrouds is tested extensively and successfully solves this issue
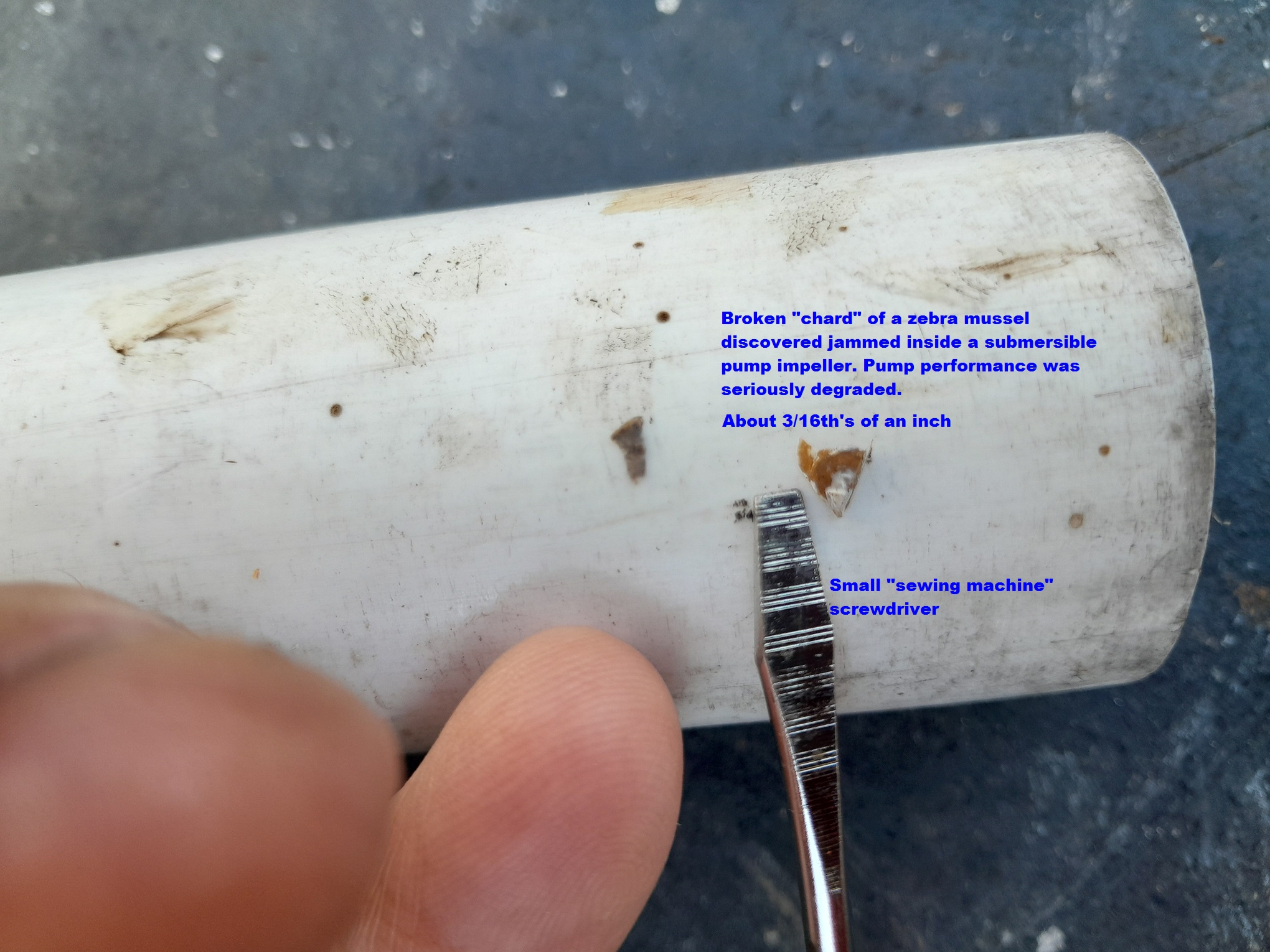
.
.
.
A note about installing Lake pumps:
Mounting pumps onto/under boat docks is not recommended, as the theft rate and the intake of weeds and debri is typically higher in the shallow water columns. This “plumber” company and our other competitors are known to install their pumps into too finely slotted filter piping shown below that was designed for downhole vertical water wells which mostly have clear well water - - not to be used for dirty lake water full of algae, weeds, and scum. We have recovered from the local lakes several of what they refer to as their “pump stands” which the proper term is a pump shroud or flow sleeve, only to discover all the too fine slots are completely clogged with scum, algae, etc. These slots are so fine that you may be able to barely slide a sheet of paper into each slot of the brand new pipe. These slotted pipes were designed for water well which is typically very clear water, not lake water with scum and weeds. Due to global warming, the water temperatures near the surface of area lakes in summertime can reach 86 or 87F, which is the high side temperature limit of pump manufacturers, water temperatures down at depth are substantially cooler leading to longer life of equipment. Special motors are available for even higher water temperatures, but no one desires to pay extra for them.
On the other hand, Lake Travis Lake Pumps has multiple exclusive innovations in our custom pump shrouds or flow sleeves that are time tested and proven:
-
All our shrouds/flow sleeves are designed to maintain a specifically engineered flow of water to allow the pump motor to remain at safe operating temperatures.
-
We use best practices to “center” the pump motor in the flow sleeve so as to prevent mud and silt accumulation from blocking proper flow of cooling water (and BTW, you can't achieve this with standard sch. 40, 4 inch PVC pipe in the region of the motor)
-
Mount the pump shroud so the pump and motor possesses more than the recommended minimum angle as recommended by the manufacturer.
-
Use a technically innovative filtration material on our uprights to yield 400% to 500% more filter area and smaller micron filter size than simple slotted PVC piping.
-
ALL our PVC shroud fittings include schedule 40 grade with minimum 200+ psi rating. We use class 160 PVC for housing the pump and motor to give better cooling flow over the motor.
-
Our competitors cannot even source this special "very hard to find" pipe - - only we have it.
-
Take note of the cheaper black colored plastic well seals on the image below (colored electrical wires emerge from these well seals). We absolutely NEVER install cheaper plastic well seals as they are almost guaranteed to come loose and "pop out" after time underwater, which destroys the intended cooling water flow required over the pump motor, we only use the tried and true more expensive cast iron well seals. Also the 4 bolts used on plastic well seals seize up after only a few months underwater so of those that don't "pop out" on their own, the ones that do persist cannot be removed, we have witnessed this first hand several times on competitors installs. If the plastic well seal cannot be pried out (rare) you are really in a pickle. The bolts used in cast iron well seals never seize on us.
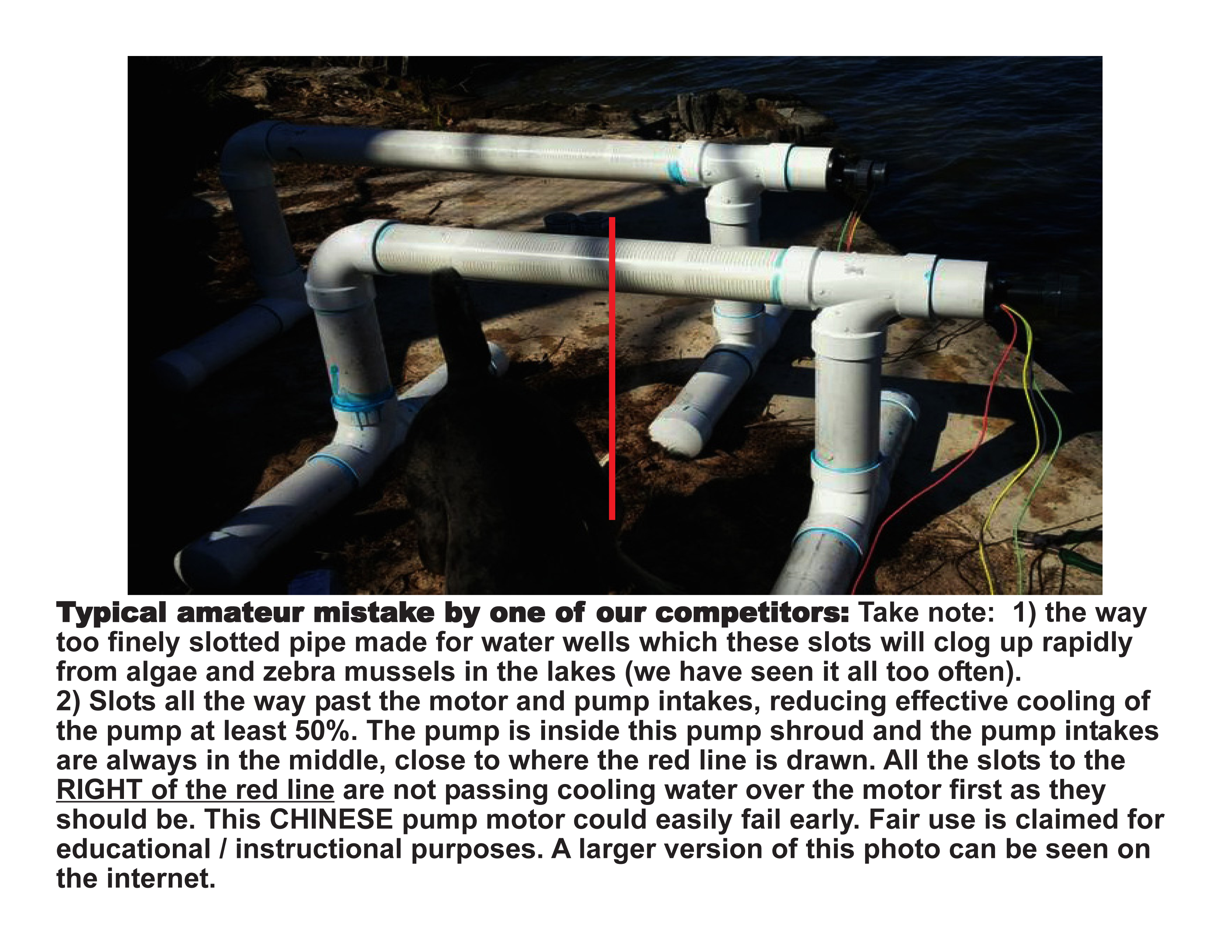
Another factor is those fine slots perpendicular to the pipe weaken it drastically. When the algae
and muck in the lake clog up these slots, then the pump is STARVED, it struggles to suction water,
this will result in cavitation bubbles, which will destroy a pump.
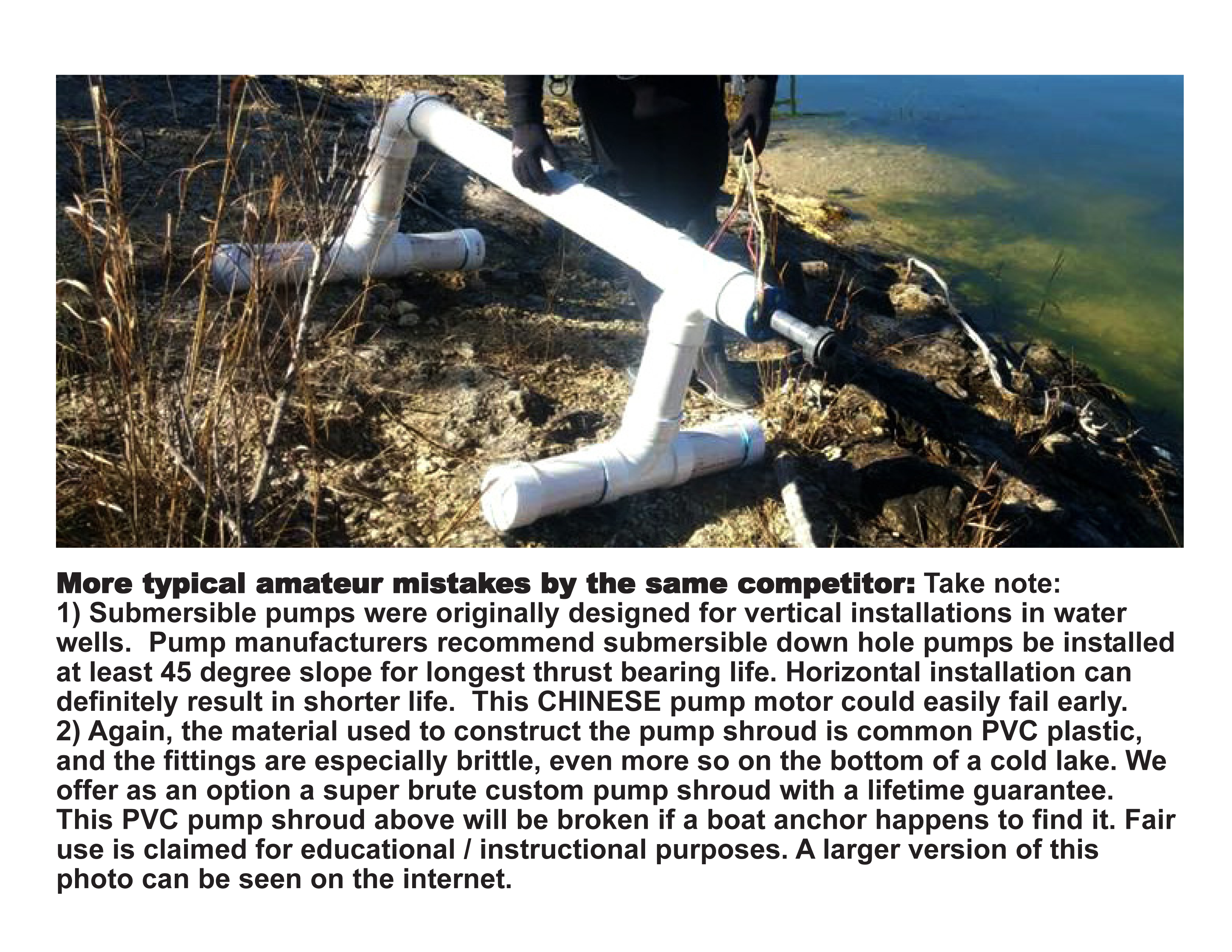
Although the image of the pump shroud above appears sloping downhill (the wrong way for the direction this pump is situated, in fact), once the shroud and pump are
installed on lake bottom at proper depth, the lake bottom is often flat .
Above is a prime example of boat prop damage to submersible lake pump cable where a local pump company
laid the pump cable and piping in too shallow of an area even though there was a deep channel nearby:
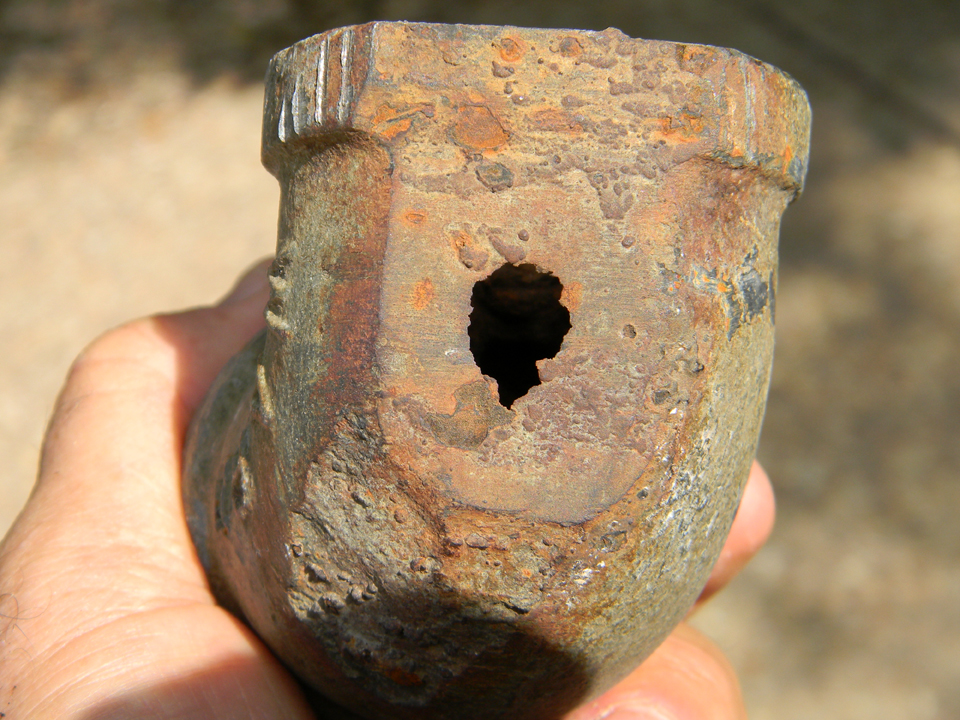
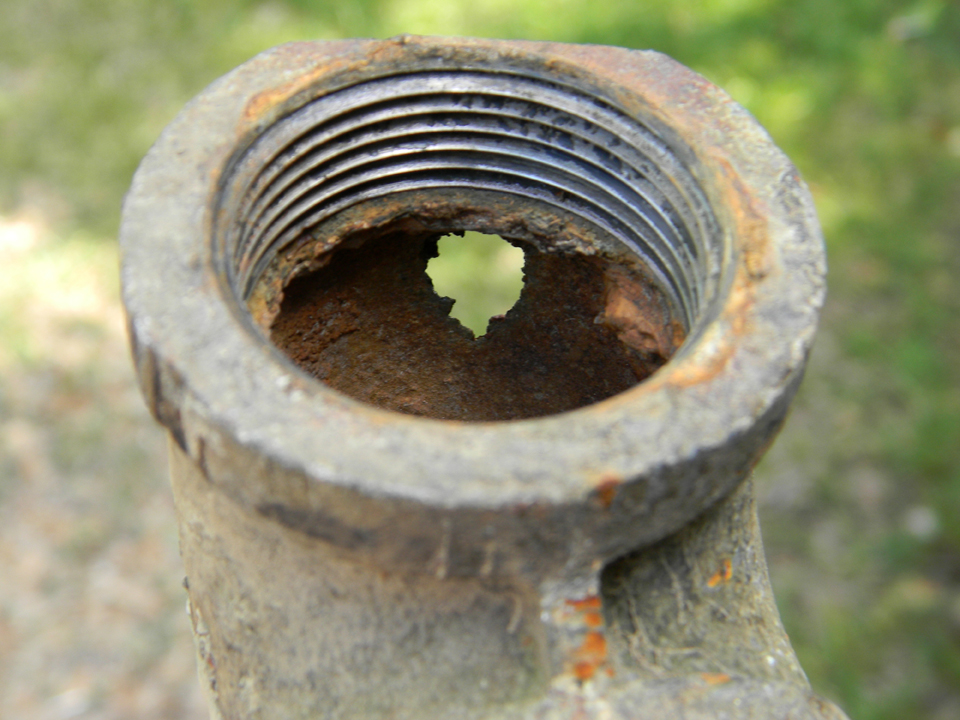
Above: even galvanized steel pipes are no match for the wear and tear of improperly secured lake pump piping.
Constant wave action against a concrete footing took it's toll over more than 25 years.
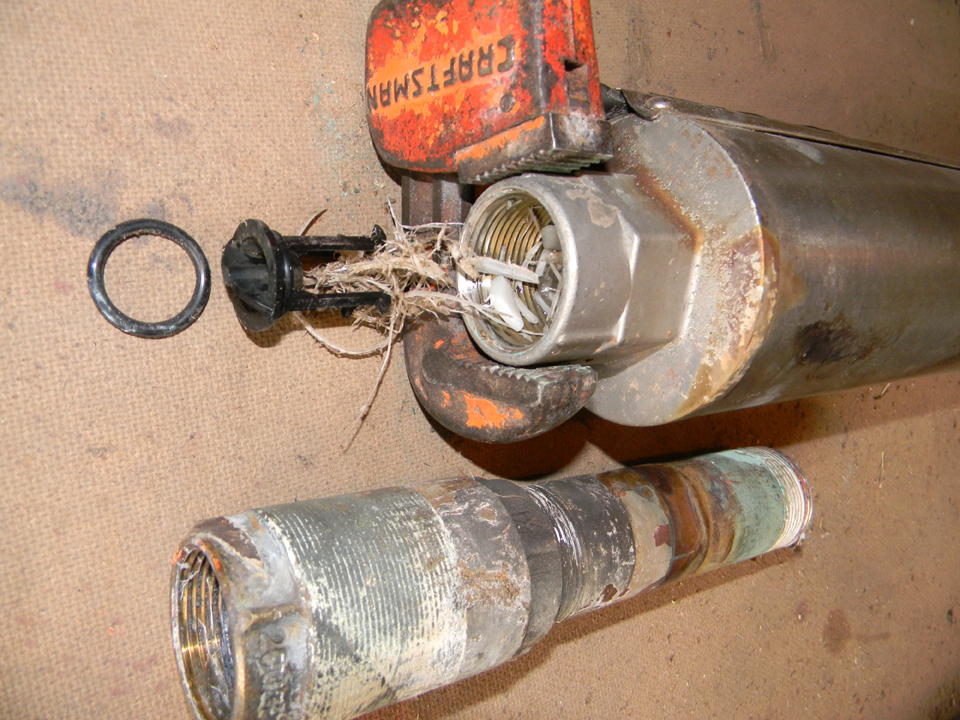
The internal check valves of pumps provided by the pump manufacturers are often not as reliable as the "aftermarket" brass check valves we install.
Above a internal check has failed.
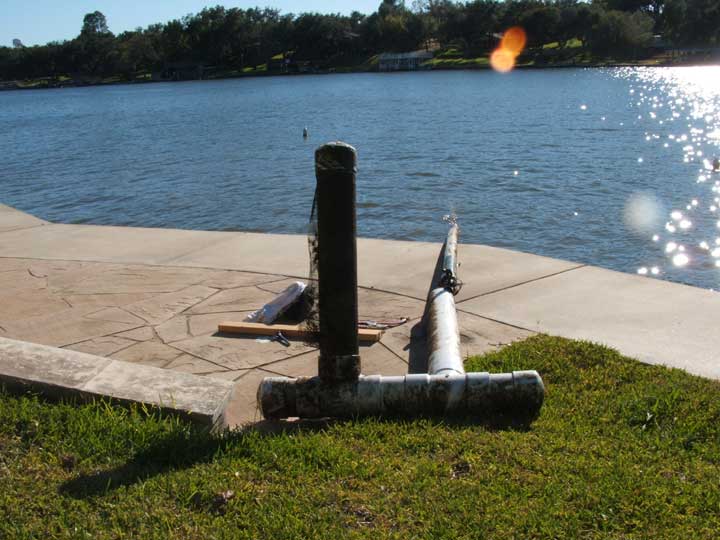
Here is a 3 HP Grundfos submersible pump installed previously by one of our competitors on lake LBJ in a rather interesting housing. The 2 inch PVC piping had come unwelded (unglued) from the 2 inch PVC male adapter threaded into the metal pump. Also the electrical wiring was precariously wrapped around the damaged area and at risk.
How could this job been done more professionally from the start ? For one, eliminate the male adapter and secondly use our proprietary PVC connection method. This area where the pump is fastened to the piping is always a high stress joint that is typically unsupported so we always "double up" on the strength by roughing the surfaces and then wrapping the PVC repair with underwater adhesive applied on composite fiber after the PVC repair was accomplished. This resulted in a super strong, more trouble free joint.
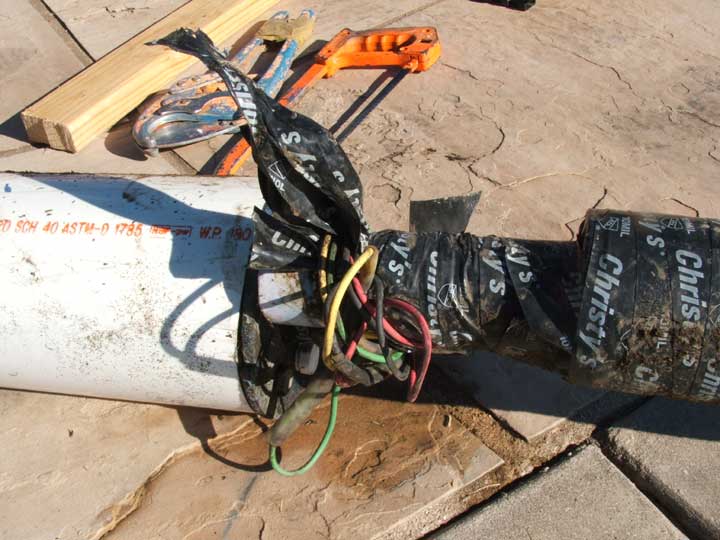
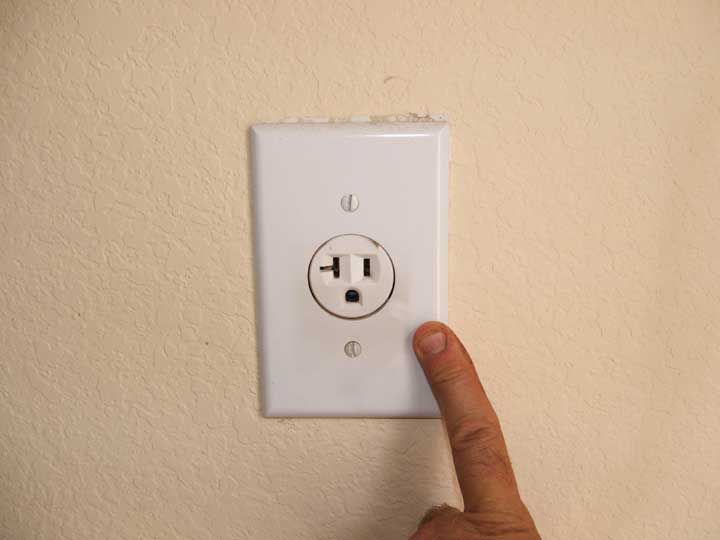
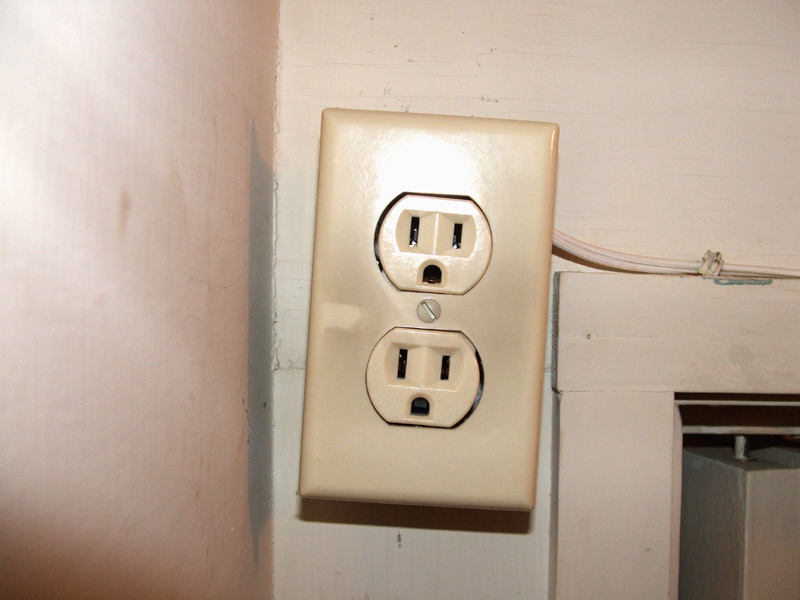
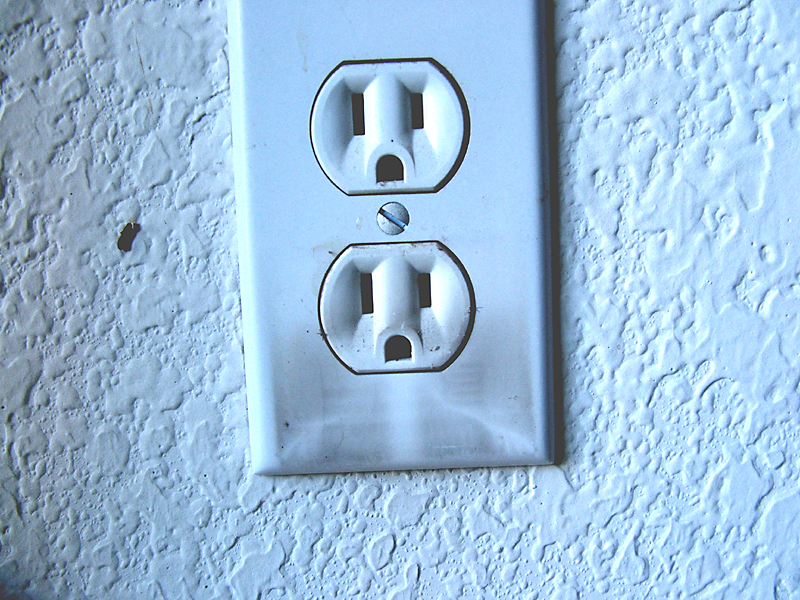
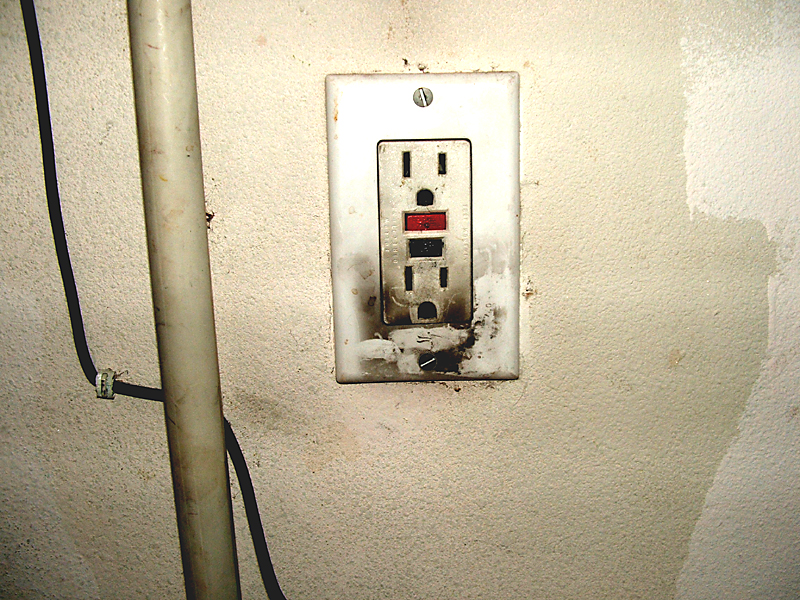
4 images above of carbon traces
We've accumulated quite a few examples of this phenomena over the years. Notice the black powder like dust on the cover ? This is evidence of a high voltage event such as a lightning strike. Irrigation controllers that were plugged into any of these outlets are "toast".
In one case we were called out for a repair the morning after a thunderstorm had rolled through the previous night. We witnessed a plug in transformer for an irrigation controller blown completely out of an electrical outlet about 28 feet across a garage.
An electrician should always be called out to dissasemble the entire wall outlet and any other affected circuits to determine the extent of any damage and repair it.
Below is the pressure release, check valve, and pressure switch component of a lake pump system installed by a competitor underground. This makes servicing it difficult.
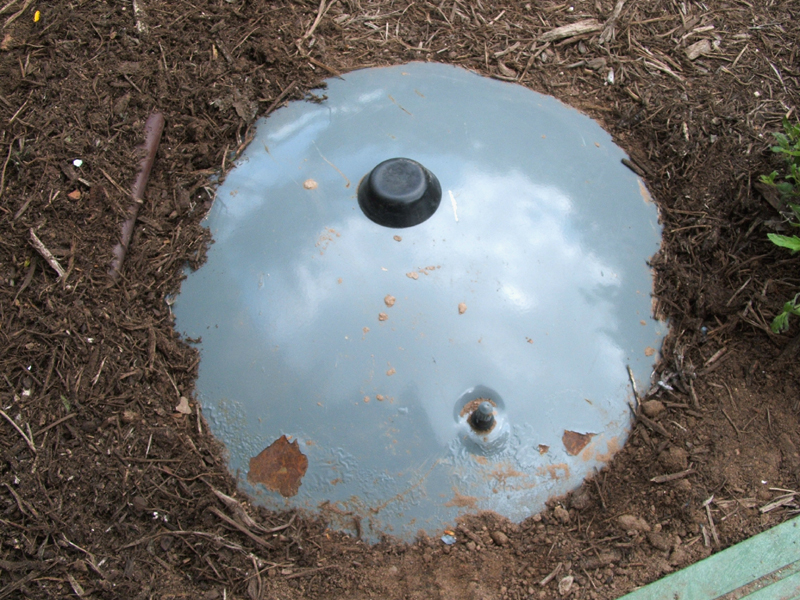
Next to the pressure switch and other components is the buried pressure tank which has already begun corroding. I would not give this installer high marks. Someday soon this is going to be an expensive repair job.
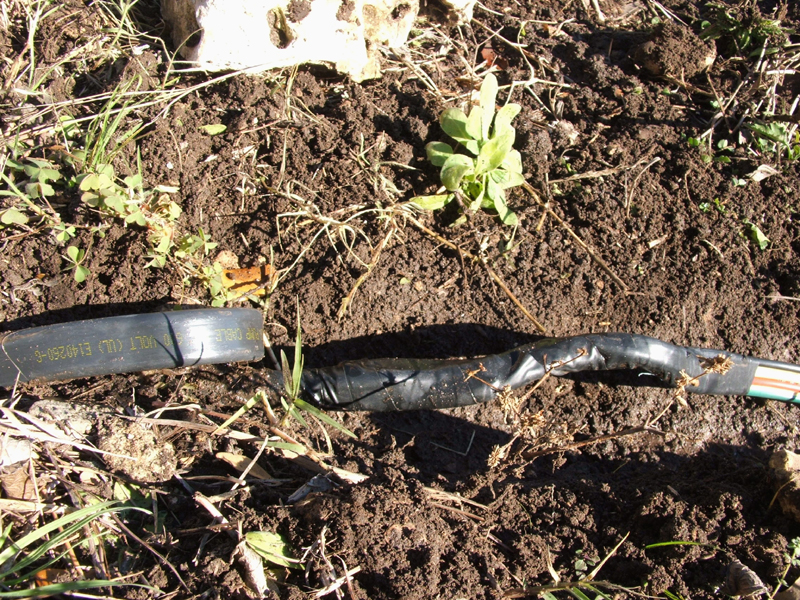
Notice above the junction of double jacketed pump cable on the left to the inferior, exposed wires type of pump cable on the right. The inferior wire on the right goes all the way down to the lake - - - hundreds of feet - - - and will fail sooner rather than later. Also note that professionals NEVER use simple electrical tape when connections are buried in the soil.
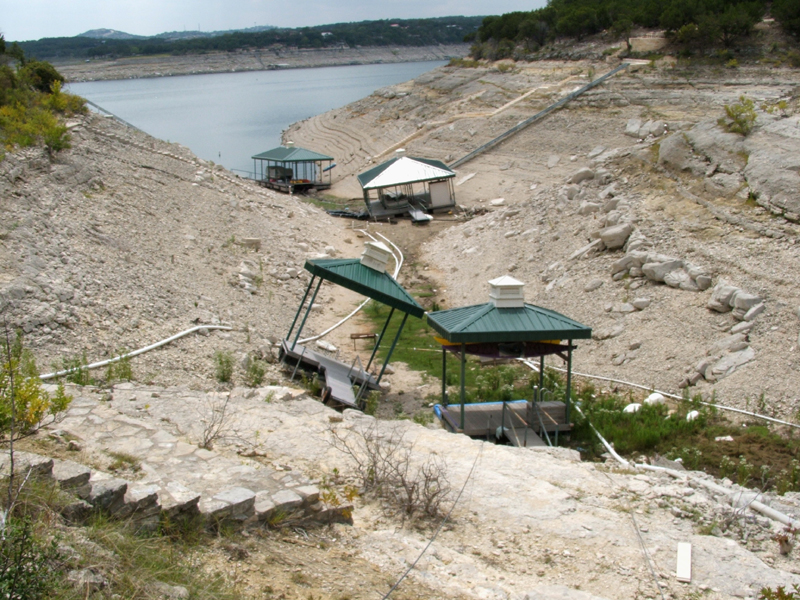
View of Lake Travis cove high and dry in September 2009 across from Lakeway area.
The installer had attempted to shield the pressure pipe and wiring inside a larger 4 inch pipe system, however, when his couplings started pulling apart he decided to use sheet metal screws to secure the couplings to the pipe. The sheet metal screws were a bit too long, and acted as "tearing points" inside to the pipe and wiring.
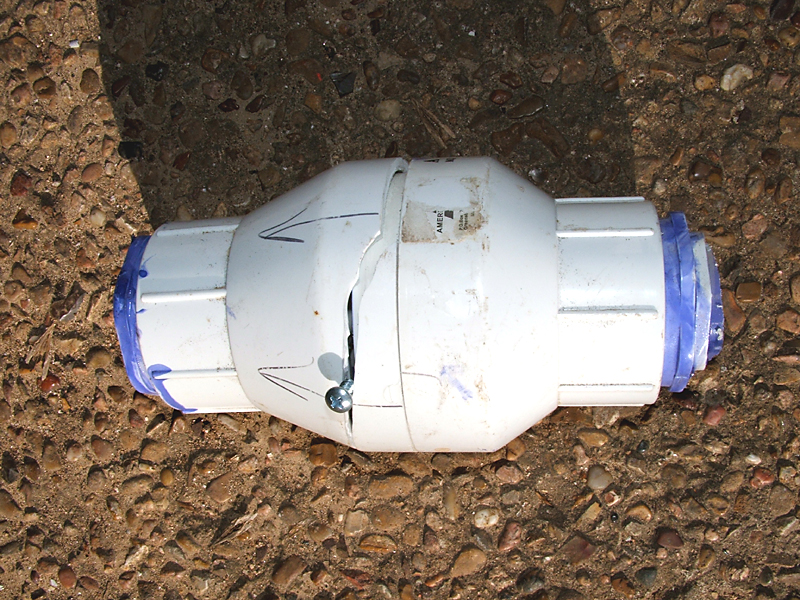
Above shows the reason why we never use PVC plastic check valves - - - they just cannot hold up. The screw is merely assisting to hold open the crack so it can be viewed more easily.
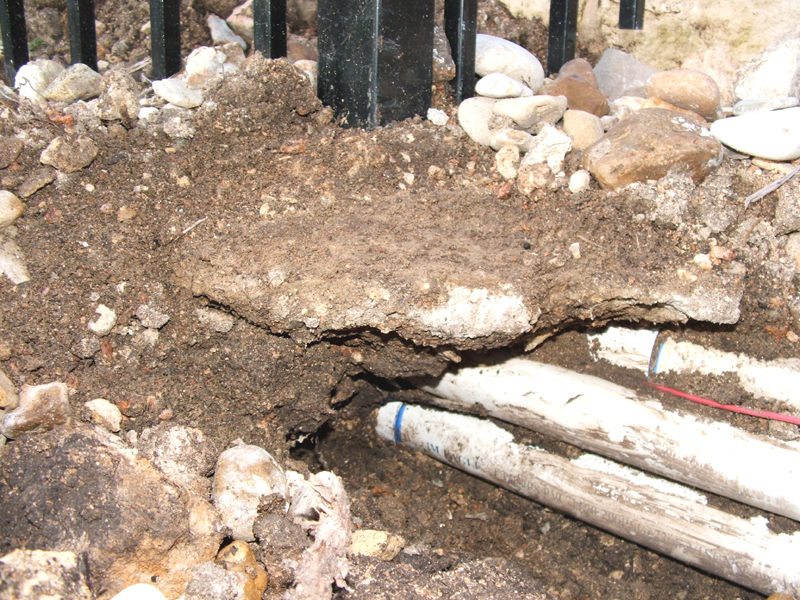
Now isn't this just peachy ? The fence installer came along some time after the irrigator and decided to just install his corner post right on top of the irrigation mains (like he did not see it when he excavated the hole).
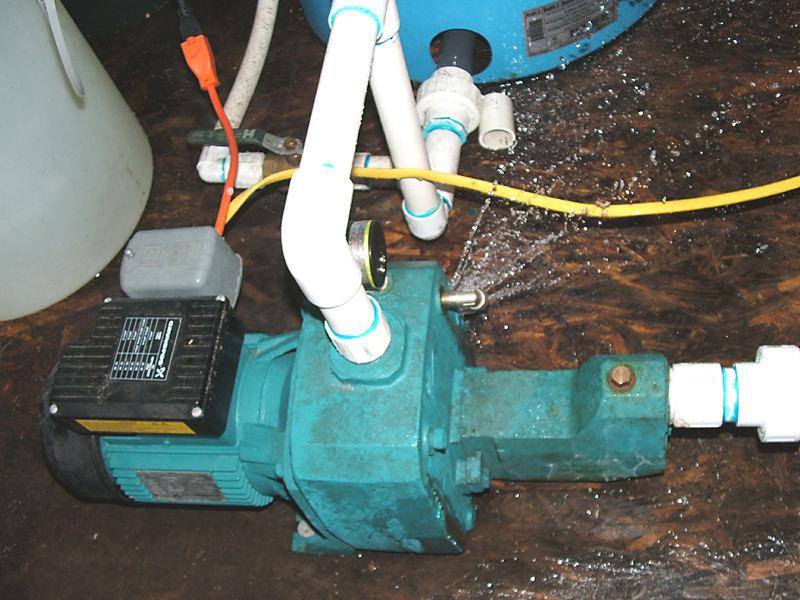
Above shows what happens to centrifugal pumps when their owners don't drain them or put added heat in the pumphouse during an extreme Texas freeze (2010). Ice actually expanded and burst the cast iron pump body.
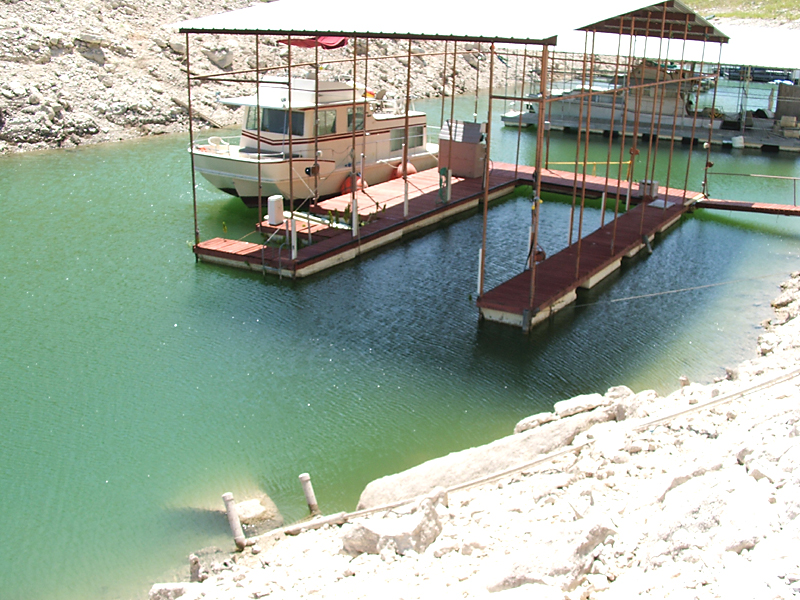
The property owners failed to monitor lake levels and the location/depth of their submersible pump which then became exposed to air. This is a sure fire way to damage a submersible pump. We also replaced all 455 feet of the substandard pump electrical cable which was starting to look dangerous.
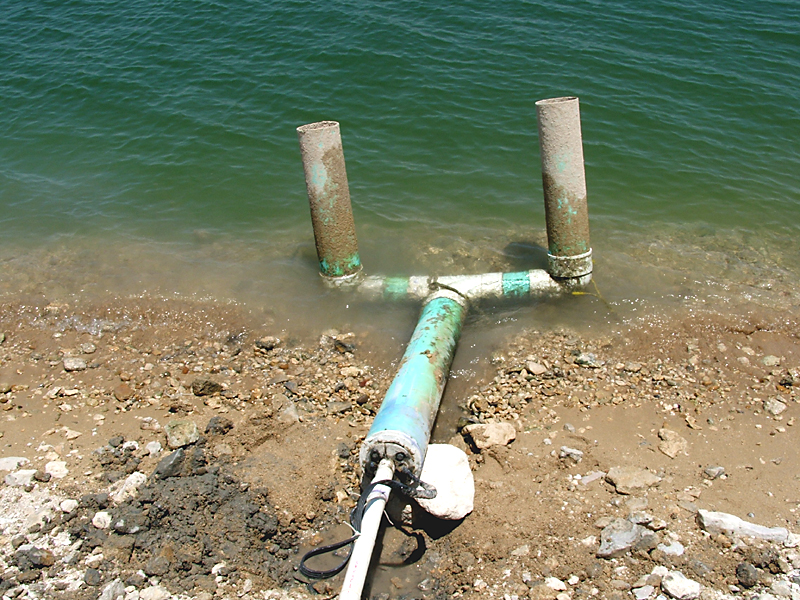
Another submersible pump on the other side of the neighborhood which suffered the same fate as the one previous. Note the vertical pipes open at the tops. What do you think will happen if a ice bag or HEB shopping bag slowly settles down to depth and is sucked into one of these pipes ? This job was installed by one of our competitors and is not the proper way to design a pump shroud.
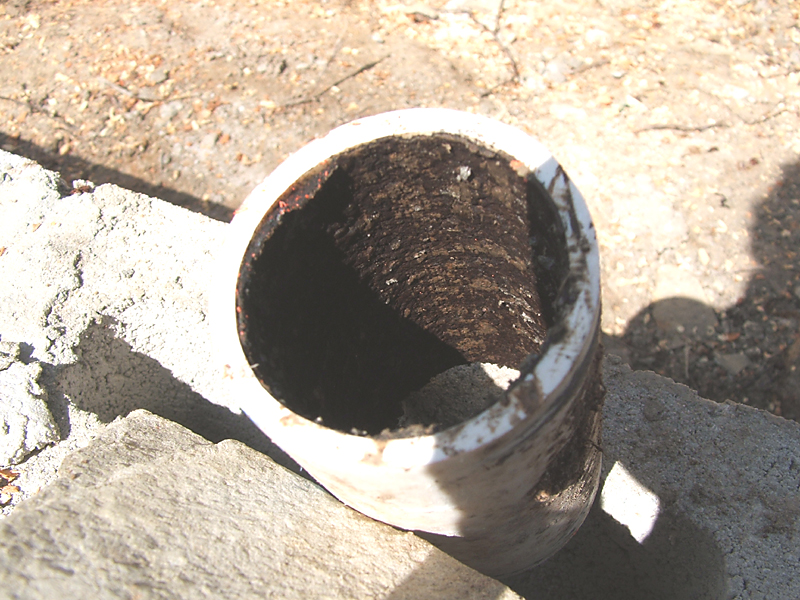
Above is what the inside of a pump pipe looks like without our advanced filter.
Sorta like atherosclerosis of arteries, eh ? All this rough accumulation inhibits the flow of water in the pipe reducing the overall performance of the system.
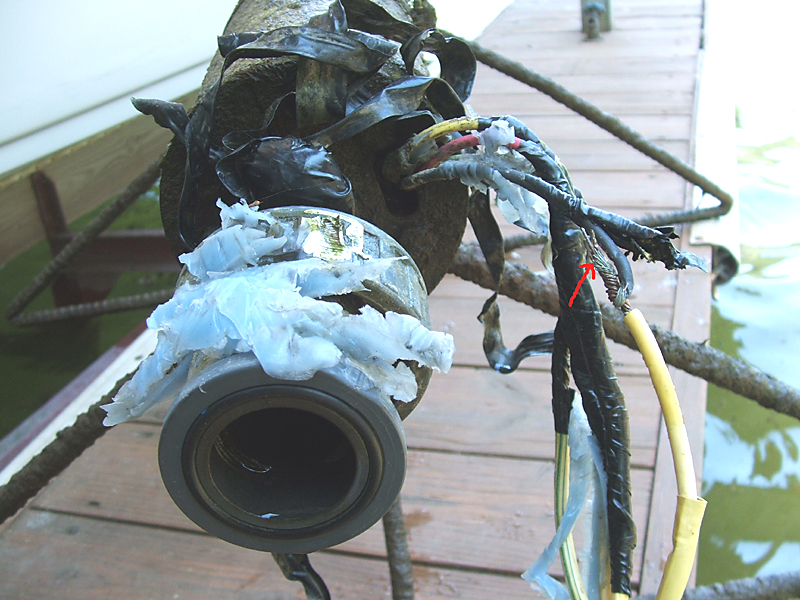
Yet another example of improper sealing of the wire connections of a lake pump. The red arrow points to the greenish oxidation of the copper.
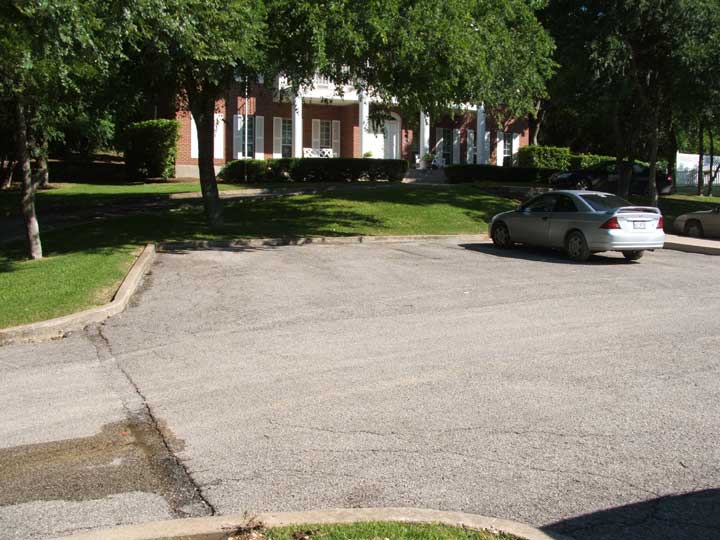
This is a sorority house. Notice the water leak in the asphalt drive ? Further examination determined that the drive had never been properly sleeved. Normally a larger pipe size is installed under all concrete and asphalt drives as a protective sleeve. Then, if a pipe fails under a concrete or asphalt surface a new pipe can merely be slid into place and solvent welded on each end. Since no sleeve existed it became a rather expensive repair.
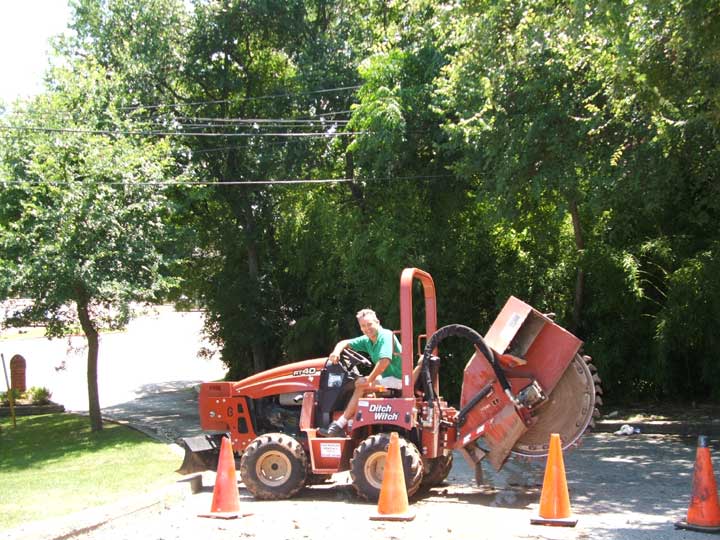
A rocksaw was employed to make the cut (below), a proper sleeve and a new pressure pipe were installed.
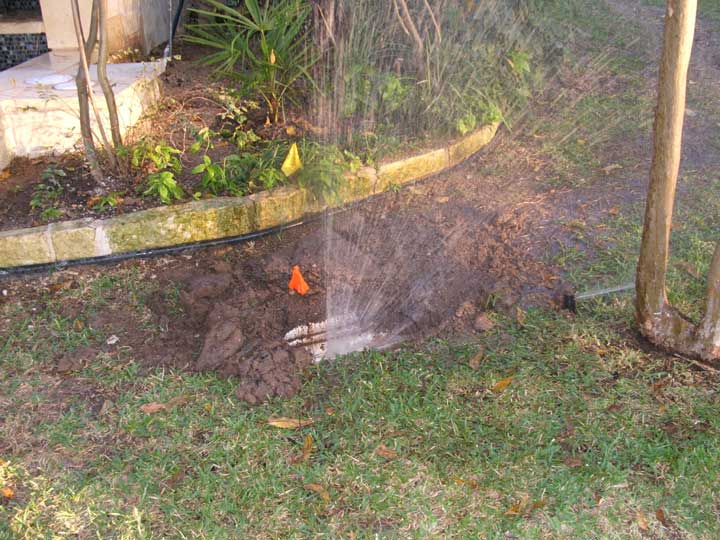
This is damage caused by a spa / pool company installation and was not discovered till the contractors had already been paid and left the jobsite. It was determined the damage was on a single pipe laid on the underneath side of a mass of pipes. The repair was made by excavating deep underneath all the pipe work so that a professional could slither in upside down on his back and examine the underside of the piping to repair the leak.
On this same property a different contractor had been employed to construct a new patio slab addition for a large barbeque pit. Only after he been paid and left was it discovered he had broken piping underneath the new slab as water gushed out from underneath this new slab whenever that zone came on. We are still waiting on a contractor to come out and saw the concrete slab so that repair can be accomplished.
Further images on the spa / pool company damage below.
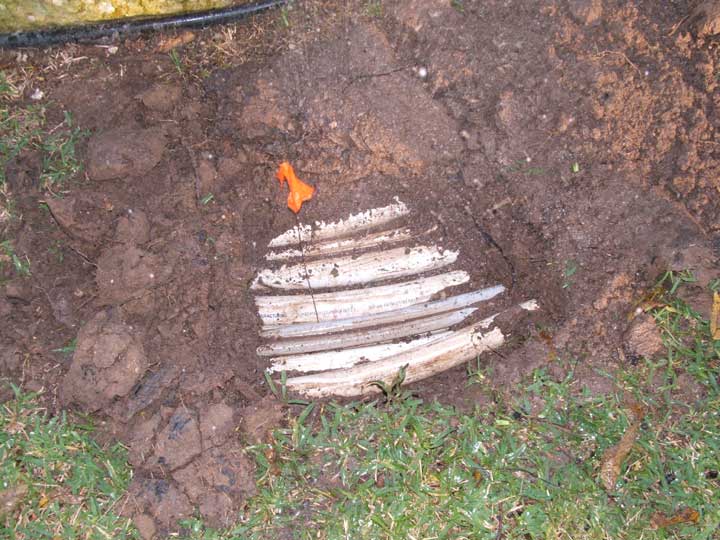
Quite a lot of pipes side by side
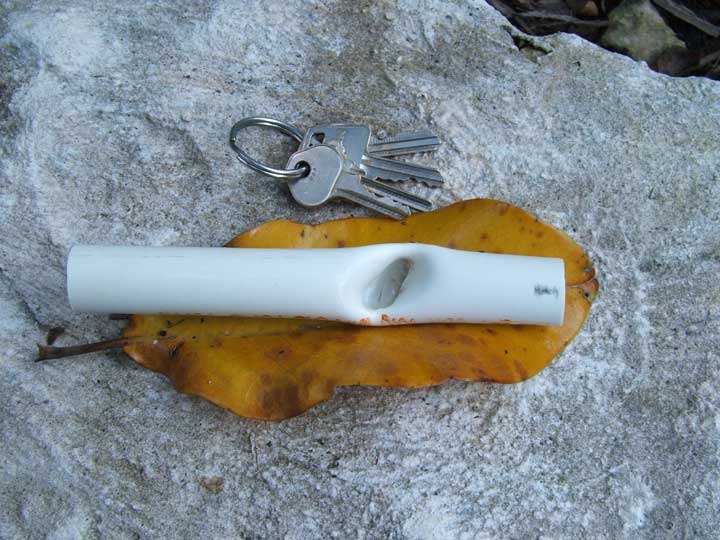
What would you guess made this hole ?
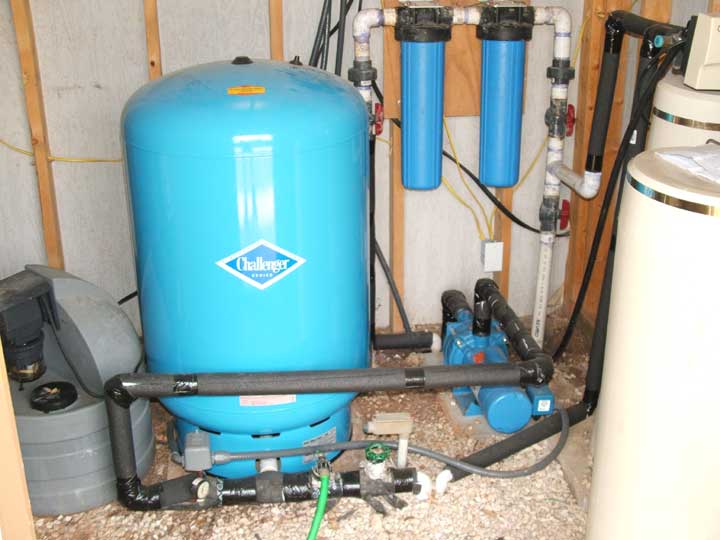
This is an image inside a well kept pump house at a beautiful residence in Wimberley on the Blanco River. We were originally called out to diagnose the system at this property. A water well tank with air bladder inside and a multi stage Goulds pump are visible, the wellhead with the submersible pump underground are not visible but are located just to the left. The small grey box with grey cables leading in and out of it is the pressure switch that controls the booster pump.
This installation was pretty clean, except the pressure gauge was a "low end" cheap model that was found by our technician to be defective and we could not locate a decent pressure relief valve for emergency high pressure situations. We also would prefer that some sort of "pump protection" device be installed in the event the booster pump exhausted the water storage tank shown below.
We don't feel it's ethical to make extra money off our customers having to sell them new replacement pumps when a simple pump protection device could have saved their pump from damage in the event of a mishap. Most property owners don't realize that a catastrophic break anywhere in their house plumbing or in the multiple underground solenoid valves, or the hundreds of feet of sprinkler system PVC mainline and PVC fittings could result in the pump running constantly trying to keep the pressure up, draining the storage tank, and then burning up the pump because it ran dry (or even intermittently dry). In a "runaway" booster pump situation, the underground submersible pump typically would not replenish the water storage tank as fast as the booster pump could exhaust the tank.
If this property is a vacation house (as this one was) pump protection becomes even more critical.
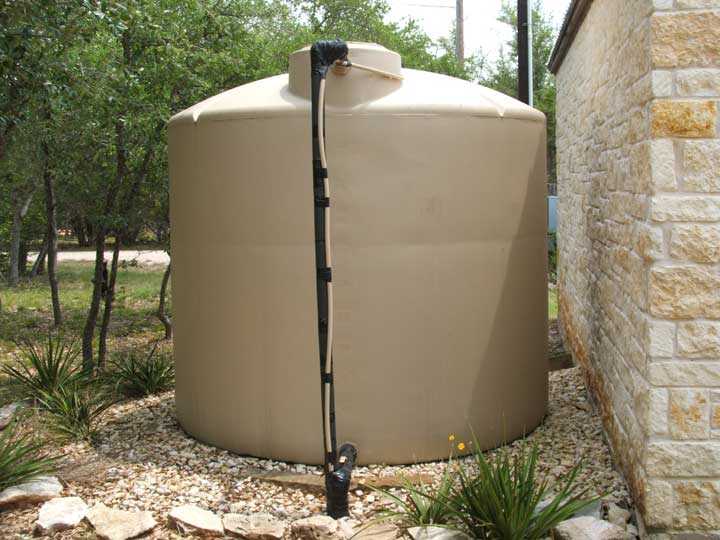
Just outside the pump house is a 2500 gallon water storage tank with a internal electrical float switch to control the submersible pump. Both the domestic water to the house and the sprinkler system obtain water from this tank.
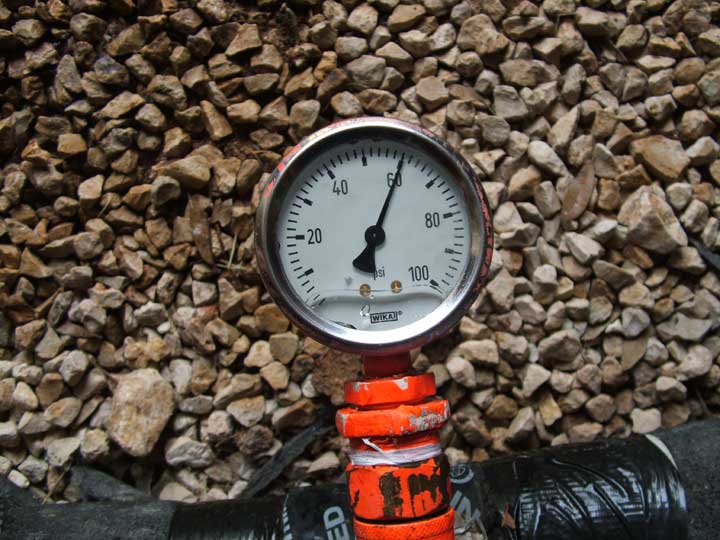
Notice the tank pressure is shown to be 60 psi at the pressure switch cut out point using a high quality glycerin filled pressure gauge. The "low end" cheap pressure gauge installed by the water well company was malfunctioning and falsely reading about 10 psi higher at around 70 psi. The tank pressure inside the well house was subject to variation because of the normal method of control which is a pressure switch. This particular pump pressure switch was set to a 40-60 range. This pressure variation disturbs the "evenness" or uniformity of how a sprinkler system applies water to the landscape and yard. We have discovered in most waterwell fed sprinkler systems, during roughly half of the time the sprinkler system is watering, the dynamic pressure obtained at the rotary sprinkler heads is often below manufacturers optimum recommendation due to this cycling of the pressure switch between low side and high side.
Rarely we discover a multistage booster pump (many are single stage) in these installations that could provide a high enough pressure so that a technician could attempt to adjust the range of the pressure switch higher. But this still does not address the constant cycling of the pump which reduces their lifespan and sells replacement pumps more often.
If the pump is rated to provide a high enough pressure, some of our competitors would just adjust the pressure switch cycle up to higher levels, but because the typical default factory settings between cut in and cut off usually range around 20 psi, this method would still result in having the high end cut out at too high a pressure in order to bring the range up high enough to have the low end at a level well above the minimum pressure level recommended by the rotary head manufacturers. Remember there are pressure losses getting from the pump house all the way to the sprinkler heads often through long distances of pipe with many fittings and a valve before finally reaching the sprinkler head. Too high a pressure will result in excessive misting which results in excessive water loss to the atmosphere and also wind drift carrying a portion of the water away from the area that is supposed to be watered. Also, too high of pressure can result in water hammer and water shock problems everytime a valve closes or the pump operates. Sometimes faucets and valves in the house start to experience water hammer at higher pressures. We have seen pumps actually start "jumping" and shaking on their concrete pads with pressure set too high. Attempting to adjust the pressure switch to reduce the range between cut in and cut out will result in unreliable operation of the pressure switch (the factory does not recommend this) as well as increase the cycling of the pump, reducing pump lifespan even more.
Be wary of anyone offering so called constant pressure valves as a solution because they will result in too high of pressure losses and therefore are not beneficial for obtaining maximum pressure with the most common type of pump used on most installations.
Solution ? We have developed a proprietary method of controlling the pump during the sprinkler cycle with the sprinkler irrigation controller that eliminates this pressure variation and provides the maximum pressure a pump can build during the sprinkler cycle when it is needed most. It also eliminates the constant cycling of the pump on and off which increases the lifespan of the pump, tank bladder, tank, pressure switch, and capacitors. This method does not disturb the domestic water pressure to the home, rather, during the time of the sprinkler system operation the domestic water pressure is actually more constant than with the pressure switch and the pressure is a bit better than normal.
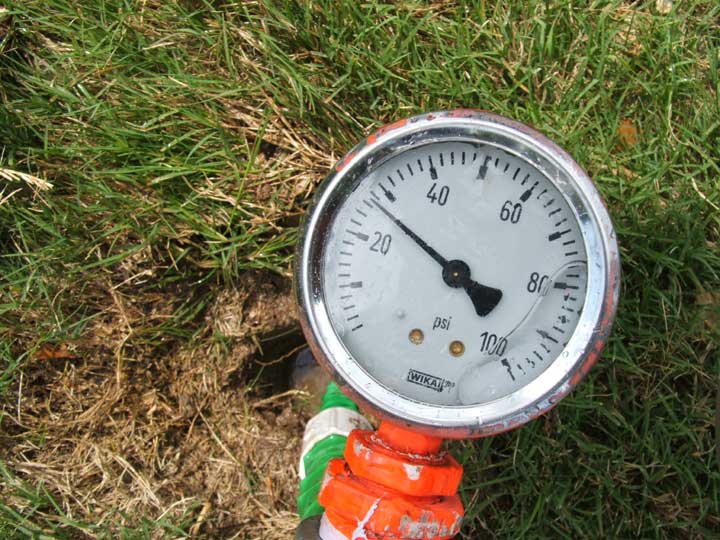
Back to the problem at hand. We determined that while reasonable pressure existed at the pump house, rather low dynamic pressure existed in critical areas, such as shown here on zone #1 which is comprised of 8 Hunter rotary heads. We have a problem here with low water pressure at the heads. More technically, there is a rather large variation between static pressure at the well tank of about 60 psi and dynamic (working) pressure at the rotary sprinkler zone #1 of only about 27 psi.
Of course, 8 rotary heads on one zone valve is usually a warning sign that an unlicensed person or do-it-yourselfer had been involved with the system. It is possible that a zone of 8 rotary heads could be accomplished using a group of smaller gallonage nozzles so as not to exceed the design gallons per minute, but in practice we never really see it. However, the unnecessary use of grey colored low angle nozzles installed in certain rotary heads on this zone had already started to tip us off as to who the "wily coyote" was that had probably installed this zone, if not the entire system.
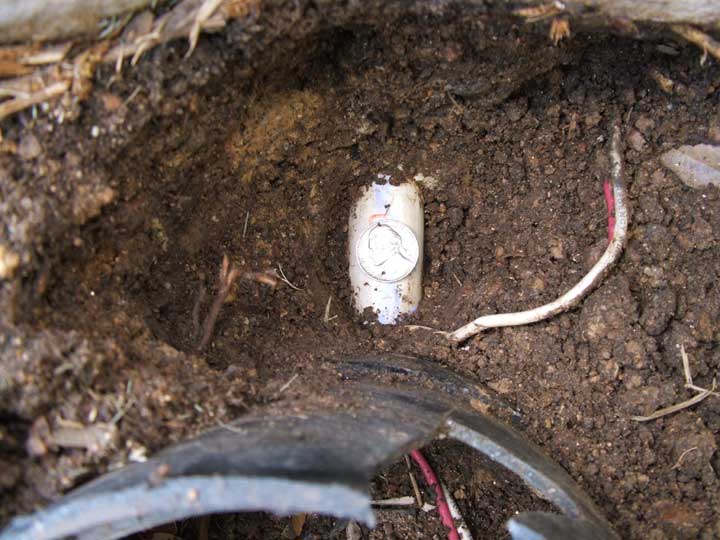
We excavated around the underground solenoid valves to determine the pipe size used to feed the valves and discovered that 3/4 inch pipe had been used which is typically too small. This image is the incoming pressure pipe feeding the valve. As it turns out, the builder drove up and explained to us that this sprinkler system was an "add to", patch work over many years and he confirmed our suspicions.
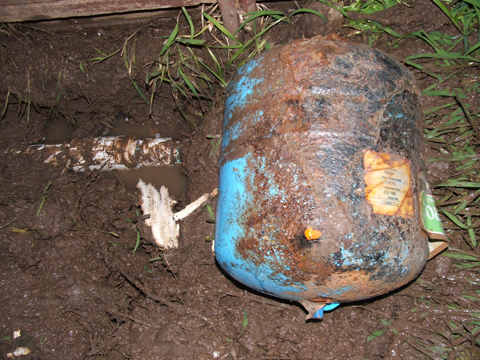
Here is an example of a well Xtrol water well bladder tank which was installed on a lake pump system inside of two white plastic bags. Did the installer really believe this was going to give extra protection from rust ?
These tanks are usually used in combination with a pressure switch to allow an "on demand" system to function properly, but this lake pump was already controlled by the irrigation controller over 300 feet up the cliff which is the preferred method. However, even though there was a water faucet to explain why an "on demand" system would be needed there was no evidence that a pressure switch had ever been installed to control this system. there was also no evidence of a manual pump switch for a water faucet.
It is conceivable this tank could have been installed to protect against water hammer. The tank was removed since it had rusted through.
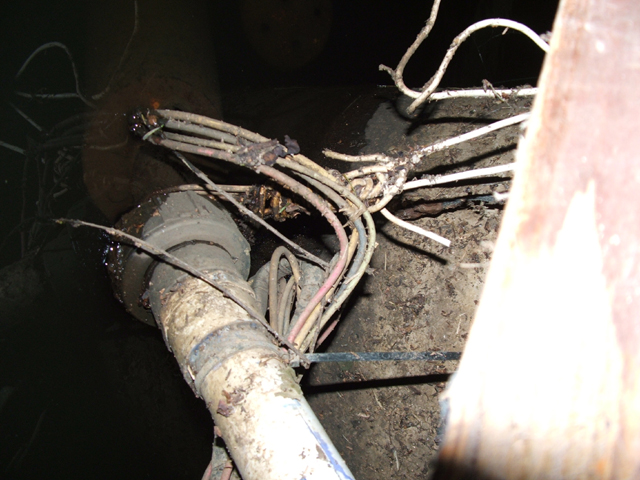
It's always amazing to me how poorly some contractors will mount a lake pump. This one had only a piece of irrigation wire and some nylon tie straps holding it to the dock underneath.
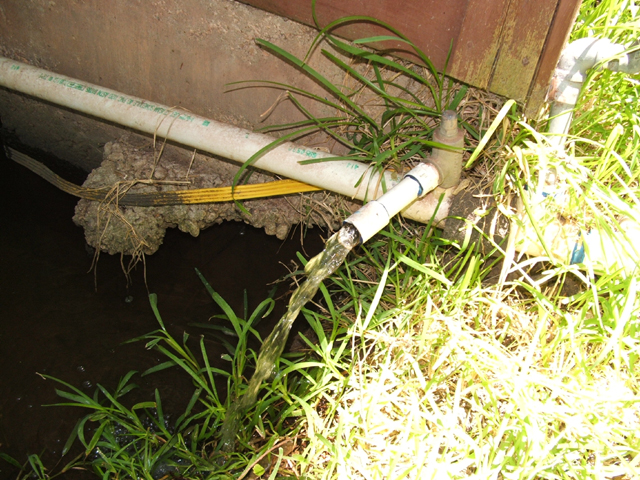
This is a defective pressure relief valve on a lake pump system which was stuck in the "always open" position. You can imagine what this does to system pressure when the pump comes on not to mention the constant loss of the column of water in the mainline (in between proper check valves) up & down the cliffside everytime an irrigation cycle is finished. Everytime the pump comes to start a cycle that column of mainline water must be refilled and it rushes up the cliffside pushing the air out until it hits the sprinkler heads at high velocity causing a shock which is not healthy for the pipe, fittings and heads. This defective pressure relief valve was replaced with a much higher quality model.
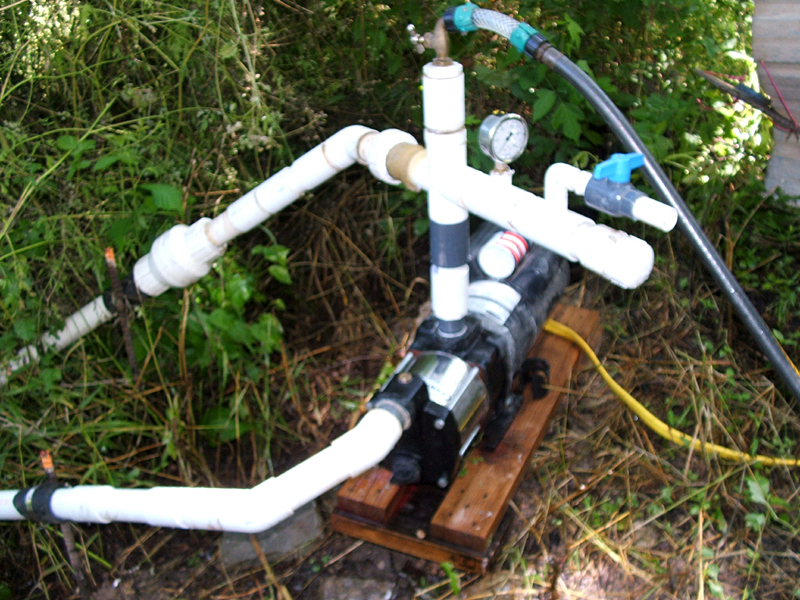
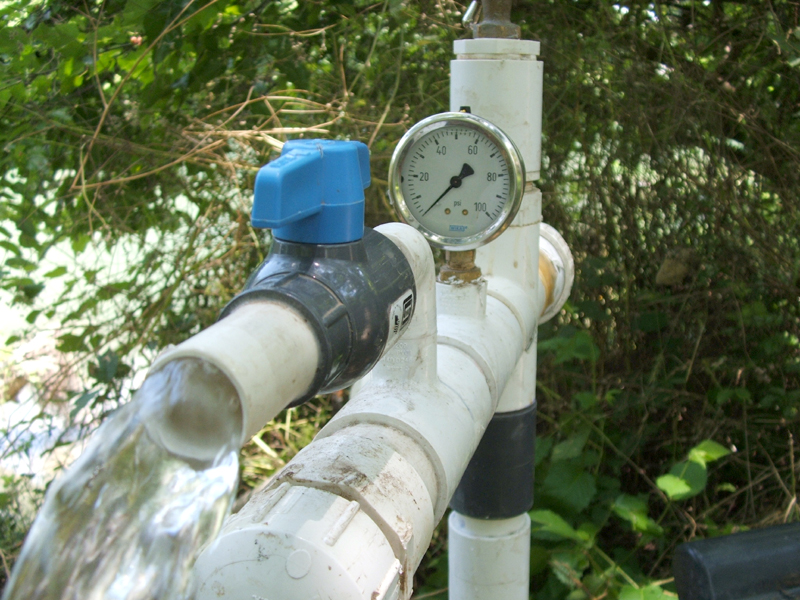
2 images above
Problem: Centrifugal pump installed by others worked fine in this location last season but would not build pressure this year:
A) Pump impellers worn or damaged ?
B) Foot valve clogged up ?
C) Suction pipe clogged or has a pinhole or crack ?
D) ?